具体业务流程如下:
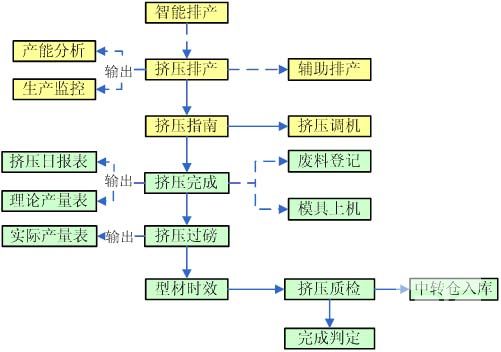
1) 通过调用销售订单资料,结合所需模具的库存状况、适用机台及机台负荷等因素进行科学排产。
2) 提供辅助排产对型材挤压的次序进行调整,实现紧急、重点型材优先进行,加强生产上的协调。
3) 跟踪挤压车间的完成情况,以避免未按制定的生产计划而盲目生产。
4) 提供对不需生产或需转其它机台生产的型材进行取消及调机功能,解决因特殊情况而作出的调整。
5) 对已挤压的型材进行过磅及时效的处理,其中过磅时可通过录入整框的总重自动计算框内各型材的重量、米重及支重。
6) 对挤压(或时效后)的型材进行质检处理,质检结果可实时跟进,并可针对需返工的数量重新排产。
7) 记录模具的上机情况,包括所用的铝棒、产出的型材、换模原因、氮化情况。
8) 型材时效管理详尽记录了整个时效过程的执行情况,方便地查询型材的入炉时间、出炉时间、时效产量及其它时效工艺的控制情况等。
9) 通过提供的各类挤压生产、产能分析、模具、铝棒使用记录等一系列报表,可以直观地了解各机台及班组的生产进度、产量、成品率等数据,以及合理地控制生产物料的耗用。
10) 提供各挤压机台的实时监控工具,监控范围包括机台的额定产能、已排产量、已完成量、未完成量、产生废品等数据,多个机台的生产情况一目了然。
11) 管理挤压车间生产材料的领用,统计车间所需的各种材料(包括铝棒、所用工具等)库存量。